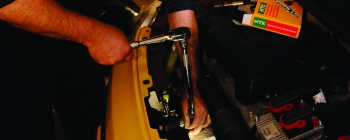
Is the ideal supplier of sensors to UK distributors
The company’s pedigree in this technology can be traced back to 1982 when supply to mainly US vehicle manufacturers (VMs) began.
By 1994 production had reached the 50 million mark and being at the forefront of this technology was fundamental to the introduction of its aftermarket sensors programme in 1997.
NGK is the world’s largest manufacturer of Lambda sensors and supplies a comprehensive range of Lambda sensors to the UK aftermarket under the NTK brand name.
The company is now an original equipment (OE) supplier to many of the world’s leading vehicle manufacturers with the same NTK parts being available to the aftermarket.
The OE-quality of its range and excellent availability coupled with its class-leading technical and sales support enables NGK to provide distributors with the necessary back-up and know-how they need to satisfy their customers and, in-turn, their garage customers’ requirements,.
Mark Hallam, NGK Spark Plugs (UK) Ltd Marketing Manager, said: “NGK has enjoyed a long and highly successful relationship with our distributors and their garage customers with our spark plug and glow plug ranges, but there are also opportunities for them to develop increased business by stocking our NTK range of Lambda and other engine management sensors including exhaust gas temperature sensors (EGTS), a product that they currently might not know too much about and may not realise the potential it offers.
“NTK Lambda sensors always match the vehicle manufacturers’ specifications. All are factory tested as part of the VMs’ specification. They have OE connectors as standard, so no crimping or soldering is required. Our NTK NOx and EGTS sensor ranges also offer the same benefits.”
NGK says distributors should help educate garages by ensuring they fit a new NTK Lambda sensor whenever they replace a vehicle’s catalytic convertor.
A worn or failed sensor can result in drastically reduced control of the fuelling system which could result in increased fuel consumption, uneven running, generally poor performance or failure of an emission test, so replacement is good news for the customer, garage and distributor.
The experience NGK has in supplying the major vehicle manufacturers worldwide allows it to offer exactly the right sensor for every vehicle application.
Checking
NGK recommends that the function of the sensor is checked every 20,000 miles or annually. The emissions check as part of the current MoT test samples the exhaust gases to monitor the efficiency of the engine, exhaust system and engine control systems. The Lambda sensor is a vital part of this system and its function is therefore influenced by many other components.
A malfunction of an associated part may directly affect the performance of a sensor. An oscilloscope and gas analyser is a much more accurate way of assessing sensor performance than relying on fault codes alone. Garages need to look for slow response times, output range and heater function.
Contaminants from poor quality oils and fuel which remain in the exhaust gases can become deposited on the sensor element affecting its operation. Even coolant from a leaking head gasket can reach the element.
Should workshops use ‘Universal’ or ‘Bespoke’ Lambda sensors?
A ‘universal’ Lambda sensor is designed to cover as many applications as possible by splicing in the connector from the unit being replaced. In theory this sounds like a good idea. In practice the potential for a mismatch with the vehicle's system or subsequent premature failure is very high.
Apart from the more obvious choices of number of wires and whether it's a zirconia or titania type there are several base sensor designs to be considered with differing characteristics including heater element performance, response time performance and even internal electrical grounding.
Once the correct choice has been made garages need to worry about making sound electrical connections and ensuring that they marry the lead wires correctly. Sensor manufacturers' wiring colours differ so garages cannot always simply join the matching colours.
For some sensors soldering the leads together is out of the question as they may need to 'breathe' through the tiny gaps in the lead wires and poor quality crimping can lead to water or oil ingress which can damage the sensor or affect its performance.
Apart from all that, if garages have not even disconnected the multiplug when splicing in the new unit they run the risk of missing such problems as corroded or damaged connector pins. In addition many vehicles now use wide band sensors and for this type there is no substitute other than the correct OE specification item.
So, for all these reasons distributors should encourage garages to always go with a bespoke OE quality Lambda sensor and steer well clear of ‘universal sensors’.
NGK says it is also essential that distributors encourage workshops to invest in the proper training to work on today’s vehicles.
Installers can also learn all about its products via the NGK interactive e-learning facility which is available on the website www.ngkntk.co.uk


