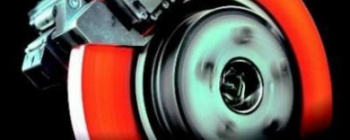
How to minimise the risk of brake judder
Apec Braking has published advice to help technicians avoid job rectification work.
Technicians are advised to pick eight equidistant points around the perimeter of the disc and to never base a determination of thickness on a single spot.
Apec say any variation in disc thickness will translate into brake judder.
Technicians must always check lateral run-out, even when fitting new discs.
Using a dial indicator, use 0.05mm to 0.10mm” as your maximum run out limit.
If you want to check run out of the discs independently of the hub, check the disc on a lathe and perform a dial indicator reading.
In an effort to remove variables from the equation, make a run out reading of the hub flange itself, without disc.
If the flange itself is causing the run out problem, you’ll be able to isolate the cause.
Finally, it is imperative when refitting wheels, that bolts are checked and in serviceable condition, check the condition of the bolts thread as well as the blots integrity.
Never use fasteners that are suspect.
Apec said: “Make sure all threaded locations are clean and free of dirt, grime or other contaminants – poor quality or unclean threads can easily result in incorrect torque readings.
“Never use an airgun to fully tighten a wheel nut or bolt, this could distort an aluminium wheel.
“The final tightening should be done with a torque wrench in the correct sequence.
“Good practice will always prevail, always service the caliper ensuring that the pad abutment points are lubricated, sliders where fitted are serviceable and working correctly and replacement springs are fitted.”
Apec also highlight the importance of correctly bedding in new discs and pads and say that garages must emphasis this to the customer.
“That conversation is nowhere near as expensive as replacing an unhappy customer’s discs and pads.” Apec added.
Garage Wire 6.9.16