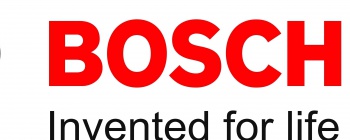
Glow Plugs and Lambda Sensors
Checking and replacing Glow Plugs for winter
Despite being key components in a modern diesel engine, the unique role of glow plugs means that motorists are far more likely to notice a fault during the colder winter months.
With over 90 years of experience and expertise in the development of the diesel engine, each generation of Bosch glow plug has led to a more highly engineered product - built for optimum performance whilst retaining the durability and reliability that the company is prides itself on. Today, Bosch develops the technology used in the latest cars and continues to invest in research and development to continue to improve this crucial product.
Underlining the importance of thorough winter checks on vehicles, healthy glow plugs not only ensure a diesel engine starts quickly and easily, but also that it will continue to run smoothly. Located deep inside the engine, glow plugs operate in the arduous conditions of the combustion chamber, across a huge temperature range, and perform for tens of thousands of miles. However, many owners remain unaware that glows plug wear, and eventually fail – so workshops have an important role to play in checking, advising and replacing when required.
To ensure that owners aren’t stranded when the cold weather hits, workshops and technicians need to check glow plugs well ahead of the winter season, and there are some easy to spot, tell-tail signs that they may need replacing. As outside temperatures begin to drop, the engine may not start as smoothly, if at all, and, even when warm, the engine may refuse to run evenly. A fall in engine power or a rise in fuel consumption, along with an increase in visible exhaust smoke, are also good warning indicators.
However, it’s not just about smooth running. Originally, glow plug systems were only used when starting a diesel engine but their role has expanded, helping a modern engine run more effectively, helping lower fuel consumption and reducing harmful exhaust gasses. Bosch glow plugs continue to glow for up to 360 seconds at the warm-up phase – reducing exhaust gasses by up to 60% compared to a cold engine.
The Bosch range of glow plugs provides the right solution for almost every diesel vehicle, covering over 90% of the global market through its international manufacturing network. Providing OE quality products for the aftermarket, it ensures that workshops can fit replacement glow plugs with confidence.
Bosch recommends that glow plugs are replaced every 50,000 to 60,000 miles (80,000-100,000 km), and it is often more economical for customers to have an entire set replaced at the same time. Once one plug has reached the end of its effective service life, it is likely that the remaining plugs also have the same amount of degradation and need to be changed as a precaution. Generally, from a labour point of view it is cheaper for a customer to have the complete set replaced rather than substituting one glow plug at a time - especially considering that the glow plugs’ wiring harness and conductor bars need to be removed during each replacement.
The Bosch range includes three variations of glow plugs; Bosch Duraterm, Bosch Duraterm High Speed and Bosch Duraspeed. Reliable in the coldest of starts, Bosch glow plugs continue to perform consistently. Made with either a metallic or ceramic elements, and with the appropriate heating element diameter, Bosch glow plugs perfectly combine a high level of resistance, operating voltage, maximum preheating temperature, heating time, and afterglow period to meet the specific requirements of every vehicle model. They also have a high resistance to chemical, mechanical, and thermal loads to provide a long service life.
Celebrating 40 years of lambda sensors
40th birthday and 1 billion lambda sensors produced since 1976
- In 1976, using a Bosch invention, Volvo first launched a car with a lambda sensor as standard equipment
- The latest Bosch lambda sensor technology is still a key component to aid control of engine emissions
- Bosch parts range provides lambda sensors in original-equipment quality for almost any vehicle
Lambda sensors are smart controllers inside the exhaust gas system: They measure the composition of the engine exhaust gases. This technology first allowed exact dosing of the amount of fuel injected therefore allowing accurate fuel and air mixture providing optimum engine operation. Now, 40 years have passed since Bosch first started the series production of this invention and the one-billionth Bosch lambda sensor left the production line. “Lambda sensors are and will remain a key element to ensure clean and efficient operation of combustion engines,”
Dr. Uwe Thomas, chairman of the Bosch Automotive Aftermarket business division, said. "The production figures at Bosch also clearly show the significant increase in demand throughout the last 40 years. It took 32 years – from 1976 to 2008 – to reach the production record of 500 million pieces, but only eight years – from 2008 to 2016 – to double the production figures to 1 billion sensors."
Successful start of production in the USA In 1976, the story of success started in the USA: The Volvo 240/260series was the first passenger car equipped with a Bosch lambda sensor as standard for the US market. Already back then, the emission regulations in the USA were relatively stringent. At the same time, the Bosch consistently demonstrated what advancements in modern engine technology could provide. Often, the emission values were even lower than the limits allowed, thanks to accurate lambda control. Today, lambda sensors have become an integral part of modern car engine management systems.
For technical reasons, more and more gasoline-powered vehicles use multiple lambda sensors per single exhaust gas system, but modern diesel vehicles are also fitted with lambda sensors. This trend will continue as the ever more stringent statutory emission limits for newly registered gasoline and diesel vehicles can only be achieved by means of a highly efficient exhaust gas treatment.
Spare parts range benefits from 40 years of production know-how As leading OE supplier, Bosch provides a wide range of the matching lambda sensor for almost any vehicle equipped with a gasoline or diesel engine for automotive workshops. This makes Bosch the worldwide leader of the automotive aftermarket – with a market coverage of 85 percent in Europe alone. The product range consists of over one thousand part numbers.
Diagnosis and replacement of lambda sensors In case of a defective lambda sensor, car drivers should have it replaced as soon as possible. Without the correctly measured oxygen values within the exhaust gasses provided by the sensor, fuel combustion loses its effectiveness and the fuel consumption increases. An On- Board-Diagnosis (OBD) test at the workshop can provide reliable information on whether a lambda sensor needs to be replaced or not. By means of the KTS- series testers and latest emission testers, Bosch provides state-of-the-art diagnostic equipment allowing a quick and reliable evaluation of a lambda sensor’s current condition. In most cases, workshops will find the right lambda sensor in OE quality within the Bosch aftermarket range. As a competent partner for workshops, Bosch provides diagnostic equipment, parts and services from a single source.