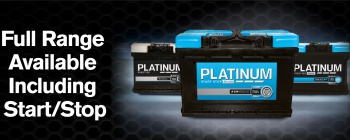
Start- Stop Technology
Many of us now take Start-Stop technology for granted, but this development has been many years in the making. As early as 1974 when Toyota tried to save fuel consumption by introducing a simple engine cut off system on certain Crown models. In the 1980’s, Volkswagen and Fiat also experimented with this. However, these were designed as a fuel cost saving exercise. The simple solution was to fit a larger battery that had the Ampere Hour capacity to cope with these demands, but it is also the cyclic capability of the battery that needs improving. None of these early Start-stop were around for very long.
Later, it was the CO2 emissions that became a major concern and this time it was a requirement from the EU to the vehicle manufacturers to manufacture vehicles that would produce far less emissions. So from 2006, the volume of cars on the road with Start-Stop technology was on the increase. It is forecasted that by the year 2020 that over 90% of new vehicles manufactured will include Start-Stop technology.
The issues with battery Ampere Hour Capacity and Cyclic Capability have been overcome by using AGM (Absorbent Glass Mat) technology which is not new, it has been around for many years as fitted on certain extreme applications as well as military applications.
A conventional car battery is only designed to start the car. Any energy used is then replenished by the vehicles charging system as the batteries work is complete. The requirement for a Start-Stop battery is not only to start the vehicle, but to be the sole supply of energy when the car is in the stop phase, so a ‘dual purpose’ product must be fitted. The demand for engine starts is also greatly increased from maybe 30,000 to well over 300,000.
An AGM battery has its electrolyte (dilute sulphuric acid) absorbed in glass matting around the internal lead plates which reduces active material shedding, the main cause of failure on this type of application. This technology also allows for the battery to cope with increased charging where regenerative braking is in operation.
Under normal operation there is no water loss due to the gas recombination properties of the product, so these batteries are fully sealed and never require topping up. Also, as a result of this there is no need for a reservoir of electrolyte above the tops of the plates, so these can now be larger. This increase in plate surface area gives greater cold starting performance. The battery can also be fitted in any orientation, an advantage on some applications.