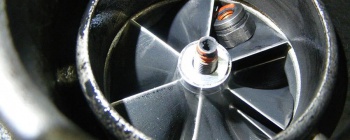
Check the turbo for a loose impeller locknut
Turbochargers are very reliable: less than 1% of turbos fail due to a manufacturing fault with the turbo itself.
95% of turbo failures are because of problems with oil starvation, oil contamination or foreign object damage.
Turbochargers can operate at speeds in excess of 6,000 revs per second (360,000 rpm), with exhaust gases up to 950°C. Each turbocharger is designed and manufactured to rotate at the correct speed for its application.
How the nuts are secured
Most turbochargers are manufactured with shafts that rotate clockwise, and shaft/impeller locknuts that have a left hand thread. Locknuts with left hand threads tend to have a self-tightening effect on the shaft. To understand this, you need to look at the two modes of turbo operation: acceleration and deceleration of the rotating assembly. The acceleration phase has by far the highest torque loading between the turbine wheel (driving) and compressor wheel (driven). During deceleration, the torque loadings are much lower as the turbo slows down.
Impeller nuts with right hand threads are perfectly satisfactory as long as the nut and shaft are in good clean condition and the correct tightening procedures are used.
Manufacturing procedure
Turbo manufacturers use ‘Poka Yoke’ fail-safe tooling fixtures and procedures to ensure the correct tightening process is carried out, with regular calibration to ensure compliance, and the calibration checked again by external examiners. The tightening procedure is: seating
torque, loosen then pre-torque and a final angle of turn to ensure correct compression of joints and shaft ‘stretch’.
This painstaking care during manufacture means that a loose impeller nut will almost certainly be due to other causes.
Causes to investigate if the locking nut is loose
• Worn bearings (usually due to oil contamination), allowing the impeller wheel to rub and ‘stall’ against the housing, loosening the locknut.
• Overspeeding (see our Overspeeding Fact Sheet) causing excessive radial expansion of the impeller wheel but shortening its length.
This relaxes the tension on the pilot shaft, and the nut spins off.
• Foreign object damage (see our Impact Damage Fact Sheet) to the compressor and/or turbine wheel, putting it out of balance.
This allows it to rub and ‘stall’ against the housing, loosening the locknut.